Common Injection Molding Defects and Their Causes
Common Injection Molding Defects and Their Causes

Introduction to Injection Molding Defects
In my 20+ years working with injection molding processes, I've witnessed firsthand how defects can derail production schedules and inflate costs. The injection molding process, while incredibly versatile and efficient, comes with its fair share of challenges. When polymers are heated, injected into molds, and cooled under pressure, numerous variables can affect the final product quality.
Understanding these defects isn't just about troubleshooting—it's about prevention. For manufacturers working with China injection molding suppliers, recognizing potential issues early can save thousands in scrapped parts and production delays. This comprehensive guide explores the most common injection molding defects, their root causes, and proven solutions to prevent them.
Whether you're a seasoned process engineer or new to the industry, this article will provide valuable insights to help you optimize your injection molding operations and improve part quality consistently.
Common Injection Molding Defects and Their Causes
1. Sink Marks
Sink marks appear as depressions or dimples on the surface of molded parts, typically occurring in thicker sections or opposite ribs and bosses. These defects happen when the outer layer of the plastic solidifies while the inner material is still cooling and contracting.
Primary causes include:
- Insufficient cooling time
- Excessive part thickness
- Inadequate packing pressure
- High melt temperature
- Poor gate location
2. Flow Lines
Flow lines manifest as wavy patterns or discoloration on the part surface, especially visible in lighter colored materials. They indicate the path the polymer melt takes as it flows through the mold cavity.
Common causes:
- Low melt or mold temperature
- Insufficient injection pressure
- Poor gate location
- Thin wall sections
- Material viscosity issues
3. Warping and Dimensional Issues
Warping occurs when different sections of a molded part cool at different rates, creating internal stresses that cause the part to bend or twist after ejection.
Key factors contributing to warping:
- Uneven cooling
- Excessive orientation in polymer flow
- Inadequate mold design (lack of uniform wall thickness)
- Improper ejection
- Material selection issues
4. Burn Marks
Burn marks appear as discolored, often brownish or black areas on the part surface. They result from material degradation due to excessive heat.
Primary causes:
- Trapped air in the mold cavity
- Excessive injection speed
- Inadequate venting
- High melt temperature
- Insufficient mold cooling
5. Short Shots
Short shots occur when the mold cavity isn't completely filled, resulting in incomplete parts. This is one of the most immediately recognizable defects in injection molding.
Common causes:
- Insufficient material injection
- Premature solidification of the melt
- Inadequate venting
- Low injection pressure or speed
- Flow restrictions in the mold
Advanced Troubleshooting for Complex Defects
Jetting and Weld Lines
Jetting occurs when the polymer melt shoots directly into the cavity rather than flowing smoothly along the mold walls. This creates snake-like patterns on the part surface. Weld lines form where two flow fronts meet during cavity filling, creating a visible line that may weaken the part.
Effective solutions:
- Modify gate design and location
- Adjust injection speed profile
- Increase melt and mold temperatures
- Implement sequential valve gating when possible
- Consider material modifications (higher melt flow index)
Flash and Burrs
Flash appears as excess material that escapes through the parting line or other mold interfaces. This thin material protrusion requires secondary operations to remove, increasing production costs.
Root causes and solutions:
- Excessive injection pressure (reduce pressure)
- Insufficient clamping force (increase clamp tonnage)
- Worn mold components (perform regular maintenance)
- Improper mold design (modify parting line or add features)
- Material viscosity issues (adjust processing parameters)
Vacuum Voids and Bubbles
Internal voids or bubbles within parts compromise structural integrity and appearance. They're particularly problematic in thick sections and can be difficult to detect without testing.
Prevention strategies:
- Increase packing pressure and time
- Optimize cooling rate
- Modify part design to eliminate thick sections
- Dry hygroscopic materials thoroughly
- Consider gas-assisted injection molding for thick parts
Material-Specific Defect Considerations
Different polymers exhibit unique behaviors during processing that can lead to specific defects. Understanding these material characteristics is essential for effective troubleshooting.
Material Type | Common Defects | Prevention Strategies |
---|---|---|
Polyethylene (PE) | Flow marks, warpage | Lower melt temperature, gradual cooling |
Polypropylene (PP) | Sink marks, warpage | Increased packing pressure, uniform cooling |
Polycarbonate (PC) | Stress cracking, bubbles | Thorough drying, moderate injection speed |
ABS | Flow lines, gloss variations | Higher mold temperature, controlled fill rate |
Nylon (PA) | Moisture-related defects, dimensional issues | Thorough drying, controlled cooling |
POM (Acetal) | Degradation, formaldehyde odor | Lower melt temperature, minimize residence time |
TPE/TPU | Surface imperfections, sticking | Mold release agents, optimized cooling |
When working with specialized plastic mold manufacturers, discussing material-specific processing requirements early in the design phase can help prevent many common defects.
Process Parameter Optimization
Injection Speed and Pressure
The injection speed profile significantly impacts part quality. Too fast, and you risk jetting, burn marks, and flash. Too slow, and you may encounter short shots, flow lines, and poor surface finish.
Best practices:
- Implement a staged injection profile (slow-fast-slow)
- Match injection speed to part geometry and material
- Monitor pressure curves for consistency
- Consider scientific molding techniques for parameter optimization
- Document successful parameters for repeatability
Temperature Management
Temperature control affects everything from material flow to part dimensions and surface quality. Both melt and mold temperatures must be carefully managed.
Critical considerations:
- Maintain melt temperature within the material's recommended range
- Ensure uniform mold temperature through proper cooling channel design
- Monitor actual temperatures, not just setpoints
- Account for shear heating during injection
- Adjust temperatures based on part geometry and wall thickness
Cooling and Cycle Time Optimization
Cooling accounts for approximately 70-80% of the injection molding cycle time. Optimizing cooling without compromising part quality is essential for production efficiency.
Effective strategies:
- Design conformal cooling channels where possible
- Implement turbulent flow in cooling channels
- Use cooling time calculators based on wall thickness
- Consider alternative cooling technologies for hot spots
- Balance cooling rate with part quality requirements
Mold Design Considerations for Defect Prevention
Gate Design and Location
Gate design significantly impacts flow patterns, pressure distribution, and potential defect formation. The gate location determines where material enters the cavity and how it fills the mold.
Design recommendations:
- Position gates in thicker sections when possible
- Size gates appropriately for material and part requirements
- Consider multiple gates for complex geometries
- Evaluate gate vestige requirements for final part aesthetics
- Simulate filling patterns before finalizing gate locations
Venting and Air Trap Prevention
Trapped air causes numerous defects including burn marks, short shots, and surface imperfections. Proper venting is essential yet often overlooked in mold design.
Venting best practices:
- Place vents at the last points to fill
- Design vents with appropriate depth (typically 0.025-0.040 mm)
- Include venting in parting lines where possible
- Consider vacuum venting for challenging applications
- Maintain vents through regular cleaning
Wall Thickness Considerations
Uniform wall thickness promotes even cooling and reduces defects like warping, sink marks, and voids. When variations are necessary, proper transitions are critical.
Design guidelines:
- Maintain wall thickness uniformity where possible
- Implement gradual transitions (3:1 ratio maximum)
- Use coring to maintain uniform wall sections
- Avoid thick sections, especially at intersections
- Consider design for manufacturability (DFM) principles early
Advanced Technologies for Defect Reduction
Simulation and Predictive Analysis
Injection molding simulation software has revolutionized defect prevention by allowing engineers to identify potential issues before cutting steel.
Benefits of simulation:
- Predict filling patterns and potential short shots
- Identify likely locations for air traps
- Analyze cooling efficiency and temperature distribution
- Estimate part warpage and dimensional changes
- Optimize process parameters virtually
Industry 4.0 and Real-time Monitoring
Modern injection molding increasingly relies on sensors and data analytics to detect and prevent defects in real-time.
Implementation strategies:
- Install in-mold sensors for pressure and temperature
- Implement automated quality inspection systems
- Utilize machine learning for process optimization
- Develop closed-loop control systems
- Track defect patterns for continuous improvement
Specialized Molding Techniques
Several advanced molding techniques have been developed specifically to address common defects in challenging applications.
Innovative approaches:
- Gas-assisted injection molding for thick sections
- Water-assisted techniques for hollow parts
- Foam injection molding for weight reduction
- Multi-material molding for complex assemblies
- Conformal cooling through additive manufacturing
Economic Impact of Defect Reduction
Cost Analysis of Quality Issues
Defects impact the bottom line in multiple ways, from direct scrap costs to hidden expenses like customer returns and brand damage.
Typical costs associated with defects:
- Direct material waste (scrapped parts)
- Machine time and labor for producing defective parts
- Quality control and inspection resources
- Rework and secondary operations
- Customer returns and warranty claims
ROI of Preventive Measures
Investing in defect prevention typically delivers substantial returns through reduced waste and improved efficiency.
Value-driven approaches:
- Implement statistical process control (SPC)
- Train operators on defect recognition and prevention
- Invest in preventive maintenance programs
- Upgrade mold design and cooling systems
- Implement simulation and analysis tools
Conclusion: Building a Comprehensive Defect Prevention Strategy
After two decades in the injection molding industry, I've found that the most successful manufacturers approach defect prevention holistically. Rather than reacting to problems, they build quality into their processes from design through production.
Effective defect prevention requires collaboration across disciplines—from part designers and mold engineers to process technicians and quality specialists. By understanding the root causes of common defects and implementing proven prevention strategies, manufacturers can significantly improve part quality while reducing costs.
Remember that defect prevention is an ongoing process. As materials evolve and part designs become more complex, staying current with industry best practices and emerging technologies is essential. Continuous improvement should be the goal, with each production run providing opportunities to refine processes and enhance quality.
By applying the principles outlined in this article, you'll be well-equipped to tackle injection molding defects proactively and deliver consistently high-quality parts to your customers.
What's Your Reaction?

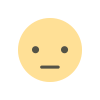




